涂裝車間智能監控系統是基于物聯網、大數據、人工智能(AI)及自動化控制技術,對涂裝生產過程進行全流程實時監控與智能管理的集成系統。其核心目標是提升生產效率、保證產品質量、降低能耗與成本,并實現車間的數字化、智能化升級。
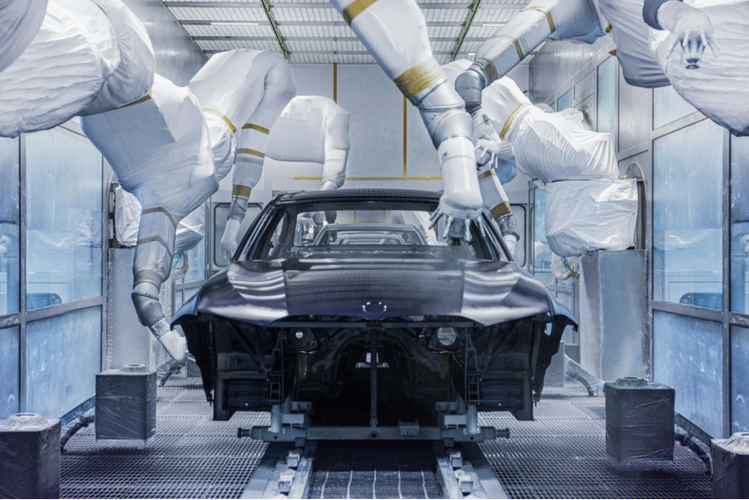
系統架構與關鍵技術
1. 數據采集層
傳感器網絡:部署溫濕度傳感器、壓力傳感器、流量傳感器、VOC(揮發性有機物)監測儀等,實時采集涂裝車間內環境參數(如溫度、濕度、風速)、設備運行狀態(如噴涂機器人運行參數、涂料供給壓力)、工藝參數(如涂料粘度、噴涂厚度)等數據。
視覺檢測設備:通過工業相機、智能視覺傳感器(如 3D 視覺系統),實時捕獲工件表面涂層質量(如流掛、橘皮、色差、顆粒缺陷),并通過圖像識別算法實現缺陷自動分類與報警。
RFID / 條碼技術:對工件、涂料桶等進行唯一標識,追蹤工件在涂裝各工序(如前處理、噴涂、烘干)的流轉狀態,實現生產過程可追溯。
2. 網絡傳輸層
工業物聯網(IIoT):通過 5G、Wi-Fi 、工業以太網等通信技術,將傳感器、設備控制器、監控終端等連接成網絡,實現數據的實時傳輸與交互。
邊緣計算節點:在車間本地部署邊緣服務器,對采集的實時數據進行預處理(如去噪、壓縮),減少上傳至云端的數據量,降低延遲,同時支持本地實時控制(如設備異常時自動觸發停機)。
3. 數據處理與管理層
工業大數據平臺:存儲與管理歷史生產數據、設備運行數據、質量檢測數據等,通過數據挖掘與分析(如時序分析、關聯規則挖掘),優化生產工藝參數(如噴涂速度與涂層厚度的匹配關系)。
人工智能算法:
預測性維護:基于設備運行數據(如振動頻率、電機電流),通過機器學習模型預測設備故障(如噴涂泵磨損、噴嘴堵塞),提前觸發維護提醒,減少停機時間。
工藝優化:利用深度學習算法分析海量工藝數據,自動生成最優噴涂參數組合(如噴槍距離、涂料流量、霧化氣壓),提升涂層均勻性與良率。
能耗管理:通過神經網絡模型優化烘干爐、空調系統的運行策略,降低能耗(如根據工件類型動態調整烘干溫度曲線)。
4. 應用展示層
智能監控界面:通過 Web 端或移動端儀表盤,實時展示車間全景(如設備狀態、生產進度、質量指標)、異常報警(如涂料泄漏、參數超閾值)、工藝參數曲線等,支持多維度數據可視化(如趨勢圖、熱力圖)。
數字孿生(Digital Twin):構建涂裝車間的虛擬鏡像,實時映射物理車間的設備運行、物流流動及生產過程,輔助工藝驗證、產線規劃與遠程調試。
移動端 APP:支持管理人員隨時隨地查看生產數據、審批工藝變更、接收報警通知,提升決策效率。
核心功能
1. 生產過程實時監控
設備狀態監控:實時顯示噴涂機器人、輸送線、烘干爐等設備的運行參數(如轉速、溫度、運行時間),異常時自動報警并記錄故障代碼。
工藝參數監控:跟蹤各工序工藝參數(如前處理液濃度、噴涂電壓、烘干時間),確保參數在設定范圍內,防止因參數波動導致質量問題。
2. 質量智能檢測與追溯
在線缺陷檢測:通過視覺系統對噴涂后的工件進行 100% 全檢,自動識別涂層缺陷并標記,不合格品實時剔除,減少人工檢測成本與漏檢率。
質量追溯:通過工件唯一標識,快速追溯其生產批次、使用涂料批次、工藝參數、設備操作人員等信息,便于質量問題定位與責任界定。
3. 智能生產調度與優化
動態排產:根據訂單優先級、設備狀態、工件類型等因素,自動生成最優生產排程,平衡各工序負荷,減少等待時間。
工藝自適應調整:針對不同工件材質、顏色、涂層要求,系統自動切換噴涂程序(如噴槍類型、涂料配方),實現柔性化生產。
4. 能源與環境管理
能耗監控與優化:實時統計車間能耗(如電力、天然氣、壓縮空氣),分析高能耗設備(如烘干爐)的運行效率,通過智能控制策略(如錯峰用電、余熱回收)降低能耗成本。
環境安全監測:實時監測車間內 VOC 濃度、粉塵含量、溫濕度等環境指標,超標時自動啟動通風系統或觸發安全警報,保障工人健康與生產安全。
5. 預測性維護與設備管理
設備健康度評估:通過振動分析、油液監測等技術,實時評估設備健康狀態,提前預警易損件(如噴嘴、密封圈)的更換需求,減少突發故障。
維護計劃自動生成:基于設備運行時間、維護歷史數據,自動生成維護計劃,并推送至維修人員移動端,實現維護流程標準化與無紙化。
免責聲明:本網站部分文章、圖片等信息來源于網絡,版權歸原作者平臺所有,僅用于學術分享,如不慎侵犯了你的權益,請聯系我們,我們將做刪除處理!
推薦資訊
產品系列