化工廠能耗管理管控系統是一種針對化工生產過程中能源消耗進行全面監測、分析、優化及控制的智能化系統,其核心目標是通過數字化技術提升能源利用效率、降低生產成本并減少環境影響。
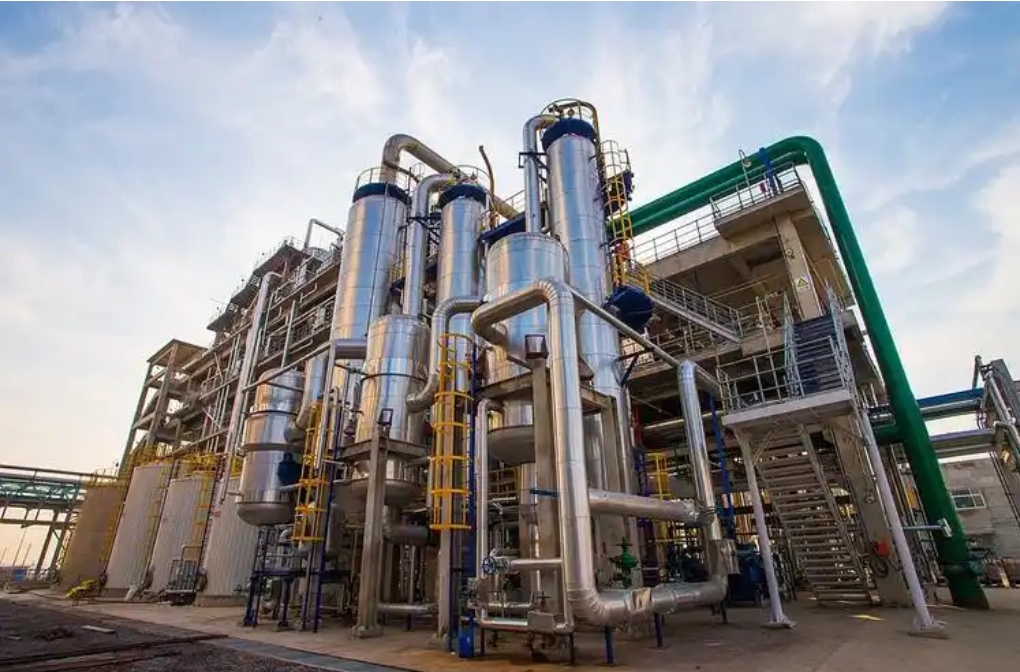
核心功能模塊
1. 能耗實時監測與可視化
多維度監測:
按車間、設備、工藝環節(如合成、精餾、包裝)劃分能耗單元,實時顯示能耗數據(如噸產品電耗、蒸汽單耗)。
動態圖表展示:通過折線圖(能耗趨勢)、熱力圖(高耗能區域分布)、儀表盤(能效指標達成率)等可視化工具,直觀呈現能耗現狀。
案例:某化工廠通過監測發現,聚合反應釜在夜間保溫階段蒸汽消耗占比達30%,通過優化保溫程序降低能耗15%。
2. 能耗分析與對標管理
統計分析:
生成日/周/月能耗報表,計算單位產品能耗(如每噸PVC電耗)、能源成本占比等KPI。
對比分析:與歷史數據、行業標準(如《石油和化工行業能源消耗限額》)或同類型裝置對標,識別節能潛力。
異常診斷:通過閾值報警(如單耗超歷史均值10%)定位高耗能設備或工藝環節,自動生成異常分析報告(如“壓縮機效率下降導致電耗上升”)。
3. 能源優化與智能控制
策略優化:
設備群控:根據生產負荷動態調整水泵、風機的運行臺數及變頻參數,例如采用“變頻+軟啟動”組合降低電機啟動能耗。
工藝協同:結合反應釜溫度、壓力與蒸汽供應數據,優化蒸汽管網調度,減少放空損失。
智能算法:
基于強化學習算法,自動優化循環水系統的流量與溫度設定值,在保證冷卻效果的前提下降低水泵電耗。
預測性維護:通過能耗數據波動預測設備故障(如換熱器結垢導致傳熱效率下降),提前安排檢修。
4. 能源成本與績效管理
成本分攤:
按車間、班組、產品維度分攤能源成本,例如將蒸汽成本按各工序用汽量比例分配至不同產品。
實時顯示能源單價波動對生產成本的影響(如天然氣價格上漲5%對甲醇生產成本的影響)。
績效考核:
設定能耗考核指標(如噸產品綜合能耗≤XXkg標煤),自動生成班組/車間的能效排名,與獎金掛鉤。
5. 碳排放管理與合規性
碳足跡核算:
根據能源消耗數據(如煤炭、天然氣用量)自動計算碳排放總量及強度(如噸產品CO?排放量)。
對接政府碳交易平臺,生成碳排放報告,滿足環保合規要求。
低碳策略建議:
推薦可再生能源替代方案(如廠房屋頂光伏電站),或優化能源結構(如用天然氣替代煤炭)。
實施價值與效益
1. 經濟效益
能耗降低:典型案例顯示,化工企業通過能耗管控系統可降低綜合能耗5%-15%,年節約電費數百萬元(如某年產10萬噸燒堿廠年節電約500萬度)。
成本透明化:通過精準成本分攤,幫助企業發現“隱形能耗”(如非生產時段設備待機耗電),減少能源浪費。
2. 管理效率提升
自動化報表:替代人工抄表與統計,報表生成時間從8小時縮短至15分鐘。
決策支持:管理層可通過移動端實時查看能耗數據,快速調整生產計劃(如電價低谷時段增加高耗能設備運行)。
3. 綠色低碳轉型
滿足“雙碳”目標要求,例如某化工園區通過系統實現碳排放數據實時上報,提前完成年度減排目標。
助力企業獲取綠色工廠、低碳產品認證,提升市場競爭力。
免責聲明:本網站部分文章、圖片等信息來源于網絡,版權歸原作者平臺所有,僅用于學術分享,如不慎侵犯了你的權益,請聯系我們,我們將做刪除處理!
推薦資訊
產品系列